Die Risikobewertung ist ein grundlegender Bestandteil des Maschinenschutzes. Ziel eines Sicherheitssystems ist es, das Risiko auf ein akzeptables Niveau zu reduzieren, wobei Risiko als Kombination aus Aufgabe und Gefahr definiert wird. Wenn Risikobeurteilung und Risikominderung ordnungsgemäß durchgeführt werden, wird das Sicherheitssystem nahtlos in die Maschine integriert. Dies ermöglicht den Mitarbeitern einen sicheren Zugang zur Ausführung ihrer Aufgaben, ohne dass sie dabei behindert werden. Ein umständliches Sicherheitssystem wird jedoch aus Gründen der Effizienz und Produktivität wahrscheinlich umgangen oder deaktiviert. Wichtig ist, dass durch die Maßnahmen zur Risikominderung keine neuen Gefahren entstehen.
Der Prozess der Risikobewertung umfasst folgende Schritte: Analyse der inhärenten Risiken der Maschine, Identifikation von Aufgaben, bei denen Menschen diesen Risiken ausgesetzt sind, und Anwendung von Risikominderungsmethoden sowie Dokumentation der Ergebnisse. Der gesamte Prozess sollte als iterativer Ansatz betrachtet werden, bei dem alle Aufgaben- und Gefahrenpaare hinsichtlich Schwere, Häufigkeit und Vermeidungsmöglichkeit bewertet werden. Das Ergebnis der Risikobewertung ist in der Regel eine Empfehlung für eine Kategorie und/oder ein Performance Level (PL), das durch die Maßnahmen zur Risikominderung erreicht werden muss.
Wird das Restrisiko als nicht akzeptabel (tolerierbar) eingestuft, sollte der Prozess wiederholt werden, um zu ermitteln, welche zusätzlichen Minderungsmaßnahmen ergriffen werden müssen. Allerdings lässt die Risikobeurteilung auch zu, dass nicht alle Risiken innerhalb vertretbarer wirtschaftlicher Grenzen beseitigt oder reduziert werden können. Ob das Restrisiko als akzeptabel eingestuft wird oder nicht, liegt letztendlich in der Verantwortung des Endbenutzers.
Der beste Ansatz für die Durchführung einer Risikobeurteilung ist die Zusammenarbeit im Team, einschließlich externer Beteiligter, um unterschiedliche Meinungen darüber einzubeziehen, welche Aufgaben auszuführen sind und welche Gefahren bestehen. Die Norm ANSI B11.0: 2020 enthält jetzt eine Liste der Verantwortlichkeiten für Lieferanten und Nutzer von Maschinen und empfiehlt potenzielle Punkte für eine Zusammenarbeit. Die Beurteilung sollte über den Schutz vor Personenschäden hinausgehen und auch Schäden an Maschinen, anderen Unternehmenswerten sowie der Umwelt berücksichtigen. Dies führt zu einem sichereren und effizienteren Arbeitsplatz.Dies bedeutet jedoch nicht, dass der Hersteller alle Risiken eliminieren kann. Der Hersteller muss verbleibende Restrisiken identifizieren und diese dem Endnutzer kommunizieren.
Schritte zur Risikoeinschätzung gemäß ISO 12100 und ANSI B11.0:
ISO 12100 und ANSI B11.0 bieten Leitlinien für den Risikobeurteilungsprozess, der aus Risikoeinschätzung und Risikominderung besteht. Die folgenden Ablaufdiagramme skizzieren die Risikobewertungsprozesse nach ISO 12100 und ANSI B11.0. Die beiden Prozesse sehen zwar leicht unterschiedlich aus, sind aber nahezu identisch.
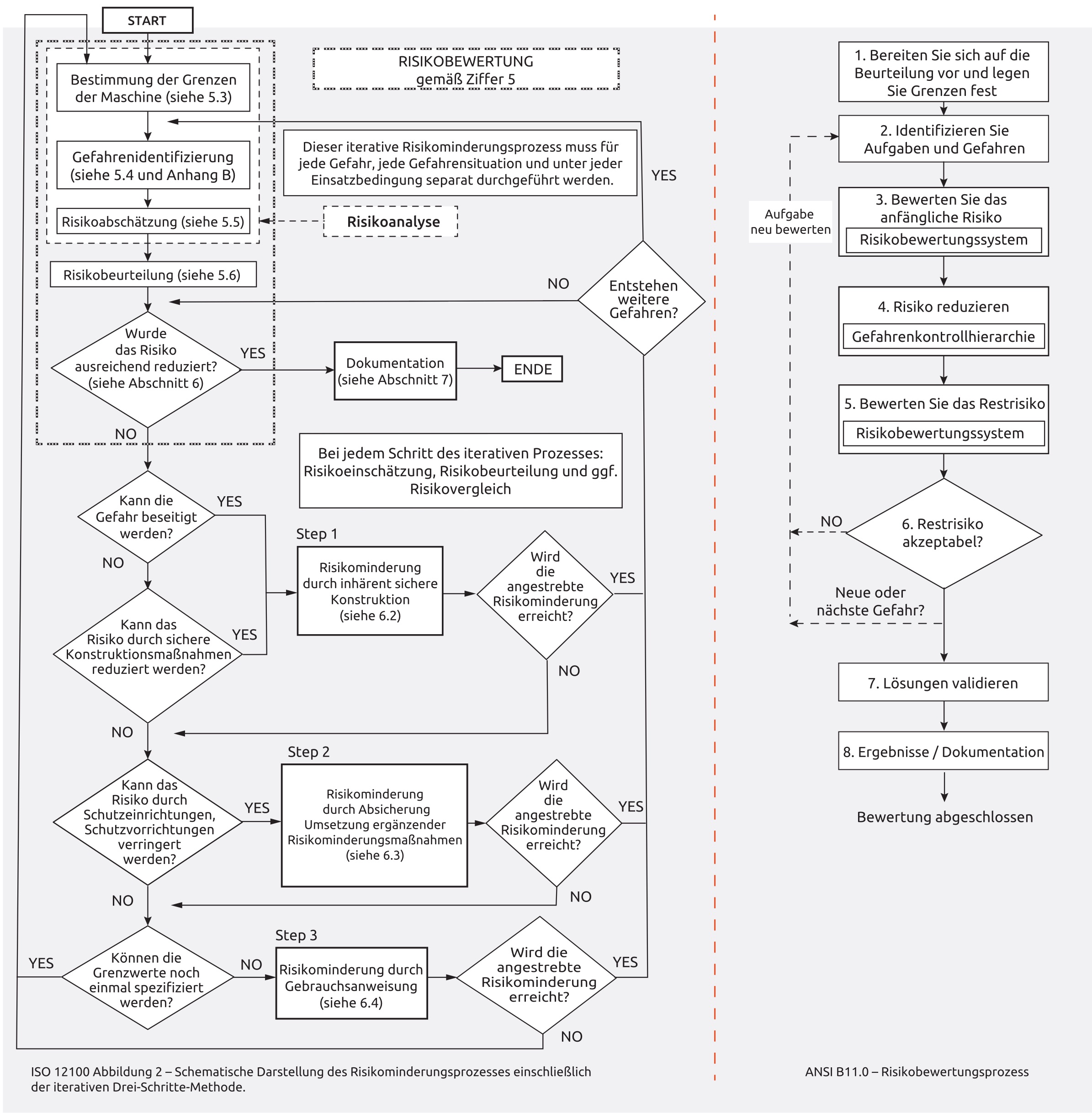
Schritt 1 besteht darin, die Grenzen und den Umfang der Maschine festzulegen und zu bewerten.
Schritt 2 besteht darin, Aufgaben und damit verbundene Gefahren zu identifizieren. Dies umfasst betroffenen Personen, die Aufgaben, die sie ausführen, und die Gefahren, denen sie ausgesetzt sind. Es ist wichtig, die Gefahren im Zusammenhang mit fluidtechnischen Teilen des Sicherheitssystems nicht zu übersehen.
Schritt 3 umfasst eine erste Risikoabschätzung, um zu bestimmen, welches Maß an Risikominderung erforderlich ist. Es stehen zahlreiche Tools zur Risikobeurteilung zur Verfügung. Die Auswahl des für Sie am besten geeigneten Tools ist ein entscheidender Schritt.
ANSI B11.0 Risikoeinschätzung
Die unten gezeigte ANSI B11.0-Risikoeinschätzungsmatrix verwendet Schweregrad und Wahrscheinlichkeit, um identifizierte Risiken zu bewerten. Es gibt jeweils vier Auswahlmöglichkeiten für die Schwere des Schadens und die Eintrittswahrscheinlichkeit. Diese sind in ANSI B11.0 Abschnitt 6.4.2 definiert.
Wahrscheinlichkeit des Eintritts eines Schadens | Schwere des Schadens | |||
---|---|---|---|---|
Katastrophal | Ernst | Moderat | Geringfügig | |
Sehr wahrscheinlich | Hoch | Hoch | Hoch | Mittel |
Wahrscheinlich | Hoch | Hoch | Mittel | Niedrig |
Unwahrscheinlich | Mittel | Mittel | Niedrig | Unerheblich |
Gering | Niedrig | Niedrig | Unerheblich | Unerheblich |
Risikoabschätzung nach ISO 13849-1
Die ISO 13849-1 hat ihre eigene Methode zur Bestimmung des erforderlichen Performance Levels (PL). Es hat drei statt zwei Faktoren; Schwere der Verletzung, Häufigkeit der Exposition und Möglichkeit zur Vermeidung; bietet aber nur zwei Auswahlmöglichkeiten für jeden Faktor. Das Risikoeinschätzungstool stellt einen erforderlichen Performance Level (PLr) a, b, c, d oder e bereit.
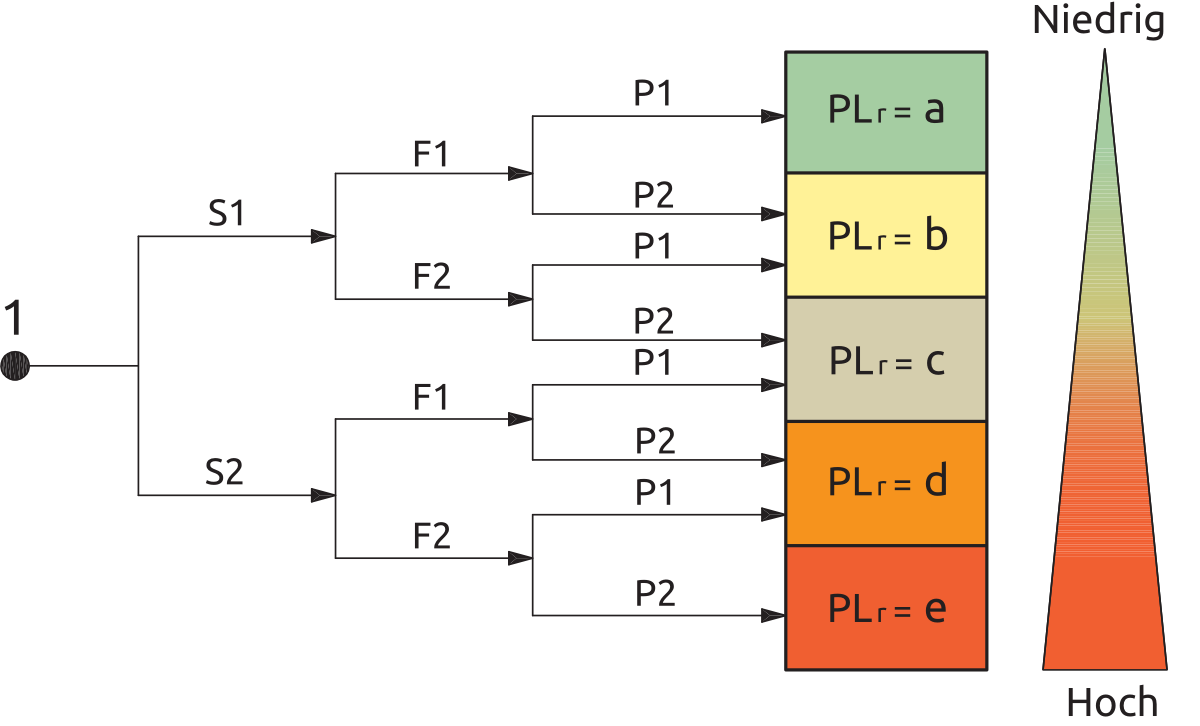
H Hoher Beitrag zur Risikominderung
Erforderliches Leistungsniveau PLr
S1 leichte (normalerweise reversible Verletzung)
S2 schwere Verletzung (normalerweise irreversible Verletzung oder Tod)
F Häufigkeit und/oder Dauer der Gefährdung
F1 selten bis weniger häufig und/oder die Dauer der Gefährdung ist kurz
F2 häufig bis kontinuierlich und/oder die Dauer der Gefährdung ist lang
P Möglichkeit der Schadensvermeidung oder -begrenzung
P1 unter bestimmten Voraussetzungen möglich
P2 kaum möglich
ANSI/RIA TR15.306 Beispiel für eine Risikoabschätzung
ANSI/RIA TR15.306 verwendet einen hybriden Ansatz, der ähnlich sowohl dem ANSI B11.0 als auch dem ISO 13849-1 Verfahren zur Bestimmung des erforderlichen Performance Levels und der Kategorie ähnelt. Es hat drei Faktoren wie die ISO 13849-1-Methodik, führt aber zu Ergebnissen, die dem ANSI B11.0-Ansatz ähnlich sind.
Eine zusätzliche Tabelle wird verwendet, um die Leistungsanforderungen zu definieren, ähnlich wie bei der ANSI B11.0-Methodik.
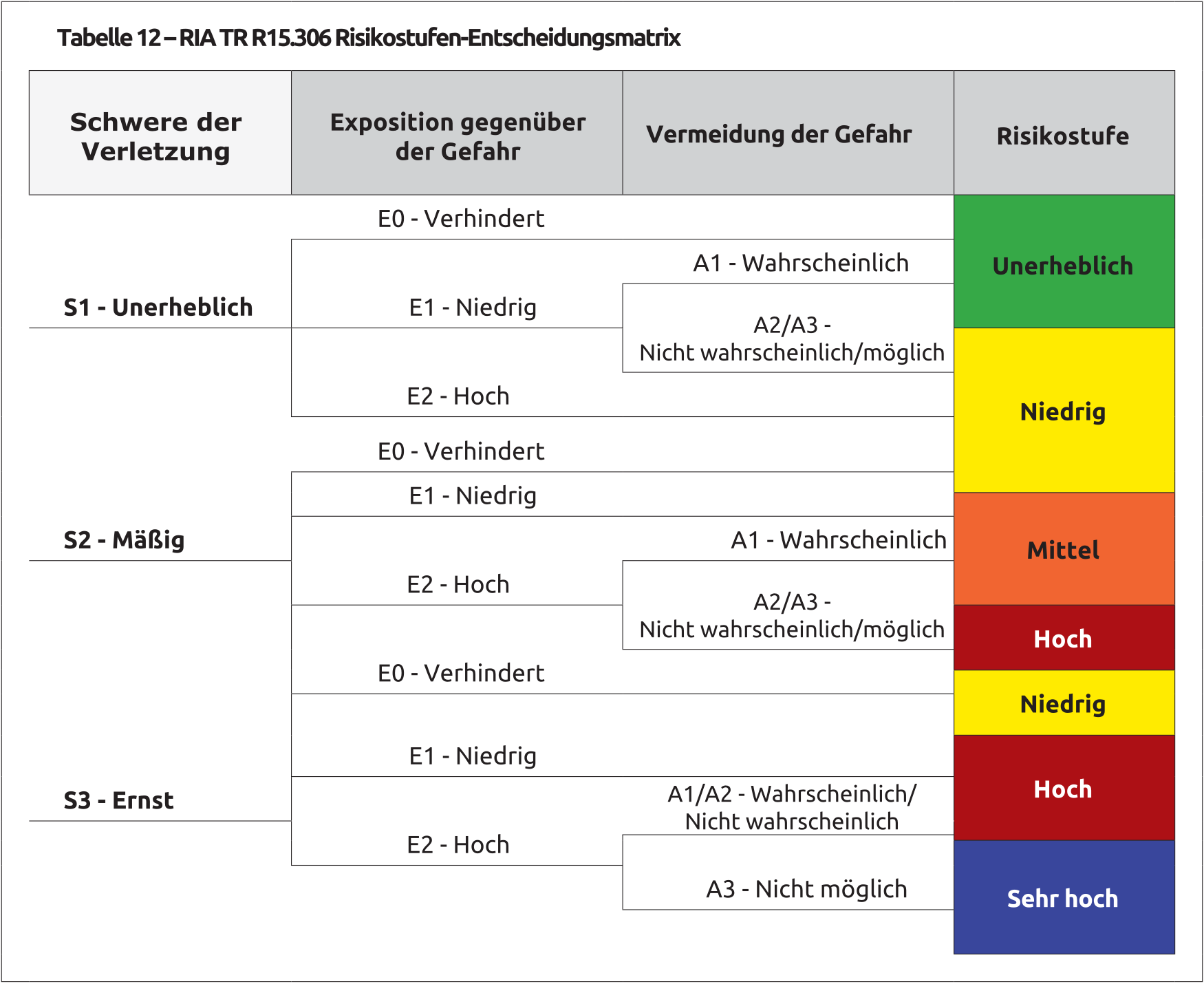
Risikostufe | SRP/CS-Mindestanforderungen | |
---|---|---|
Pl R | Structure Category | |
Unerheblich | c | 1 |
Niedrig | c | 2 |
Mittel | d | 2 |
Hoch | d | 3 |
Sehr hoch | e | 4 |
Risikobeurteilung der Fluidtechnik
Zu beachten:
- Löst ein pneumatisches oder hydraulisches System eine Bewegung aus?
- Könnte das pneumatische oder hydraulische System Quetsch-, Scher- oder Einstichstellen verursachen?
- Kann das Abschalten des pneumatischen oder hydraulischen Drucks dazu führen, dass sich Dinge bewegen?
- Könnte die Schwerkraft einen Einfluss haben?
Wenn Quetschstellen, Scherstellen und Einstichstellen durch fluidtechnische Geräte vorhanden sind, müssen diese Gefahren behoben werden. Nehmen Sie sich Zeit, um die möglichen Fehlermodi der im System verwendeten Ventile zu verstehen; und die Schwere der Gefahren basierend auf den im pneumatischen oder hydraulischen System wirkenden Drücken und Kräften.
Jeder fluidtechnischer Antrieb (Zylinder oder anderweitig) im System der Maschine muss hinsichtlich seiner Steuerung und der angewendeten Drücke bewertet werden, um die Kräfte zu bestimmen, die erzeugt werden können. Anschließend muss das Steuerungsschema der Ventile im System untersucht werden, um sowohl normale als auch fehlerhafte Zustände des Fluidkreislaufs zu ermitteln. Schließlich ist es wichtig zu berücksichtigen, was passiert, wenn ein Sicherheitsereignis eintritt. Daher ist es wichtig zu bestimmen, was die Antriebe tun, wenn die Ventile stromlos sind oder ein Fehler auftritt.